080603_CoLab: R&Sie + THEVERYMANY (001)
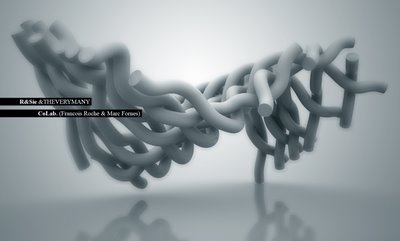
Collaboration with Francois Roche, principal of R&Sie (www.new-territories.com)& THEVERYMANY / February 2008
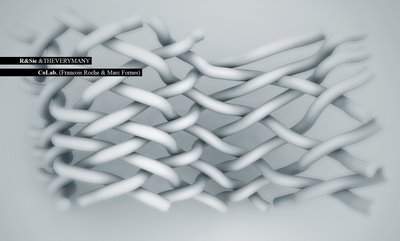
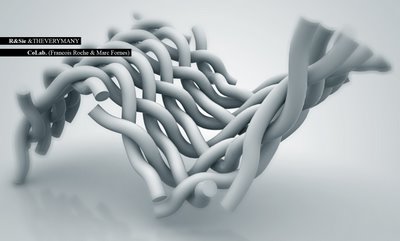
THEVERYMANY was initially asked to developed a plug-in looking at weaving structures - first from a series that post is showing the very first generic tests.
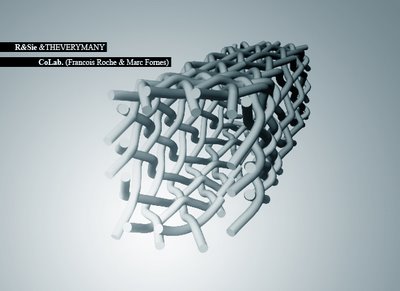
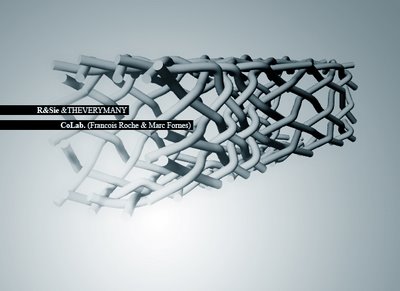
Side notes: WEAVING (ie wikipedia.org)
WEAVING is the textile art in which two distinct sets of yarns or threads, called the warp and the filling or weft (older woof), are interlaced with each other to form a fabric or cloth. The warp threads run lengthways of the piece of cloth, and the weft runs across from side to side.
Cloth is woven on a loom, a device for holding the warp threads in place while the filling threads are woven through them. Weft is an old English word meaning "that which is woven".
The manner in which the warp and filling threads interlace with each other is known as the weave. The three basic weaves are plain weave, satin weave, and twill, and the majority of woven products are created with one of these weaves.
Woven cloth can be plain (in one color or a simple pattern), or it can be woven in decorative or artistic designs, including tapestries. Fabric in which the warp and/or weft is tie-dyed before weaving is called ikat. Fabric decorated using a wax resist method is called batik.
The ancient art of handweaving, along with hand spinning, remains a popular craft. The majority of commercial fabrics, in the West, are woven on computer-controlled Jacquard looms. In the past, simpler fabrics were woven on dobby looms and the Jacquard harness adaptation was reserved for more complex patterns. Some believe the efficiency of the Jacquard loom, and the Jacquard weaving process makes it more economical for mills to use them to weave all of their fabrics, regardless of the complexity of the design.
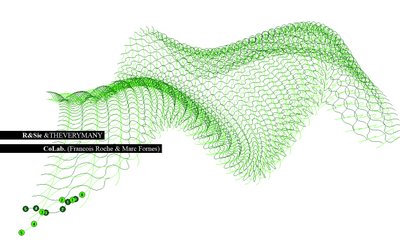
WEAVING / PROCESS
In general, weaving involves the interlacing of two sets of threads at right angles to each other: the warp and the weft. The warp are held taut and in parallel order, typically by means of a loom, though some forms of weaving may use other methods. The loom is warped (or dressed) with the warp threads passing through heddles on two or more harnesses. The warp threads are moved up or down by the harnesses creating a space called the shed. The weft thread is wound onto spools called bobbins. The bobbins are placed in a shuttle which carries the weft thread through the shed. The raising/lowering sequence of warp threads gives rise to many possible weave structures from the simplest plain weave (also called tabby), through twills and satins to complex computer-generated interlacings.
Both warp and weft can be visible in the final product. By spacing the warp more closely, it can completely cover the weft that binds it, giving a warpfaced textile such as rep weave. Conversely, if the warp is spread out, the weft can slide down and completely cover the warp, giving a weftfaced textile, such as a tapestry or a Kilim rug. There are a variety of loom styles for hand weaving and tapestry. In tapestry, the image is created by placing weft only in certain warp areas, rather than across the entire warp width.
Labels: Francois Roche, marc fornes, rhinoscript, rhinoscripting, RSie, theverymany
<< Home